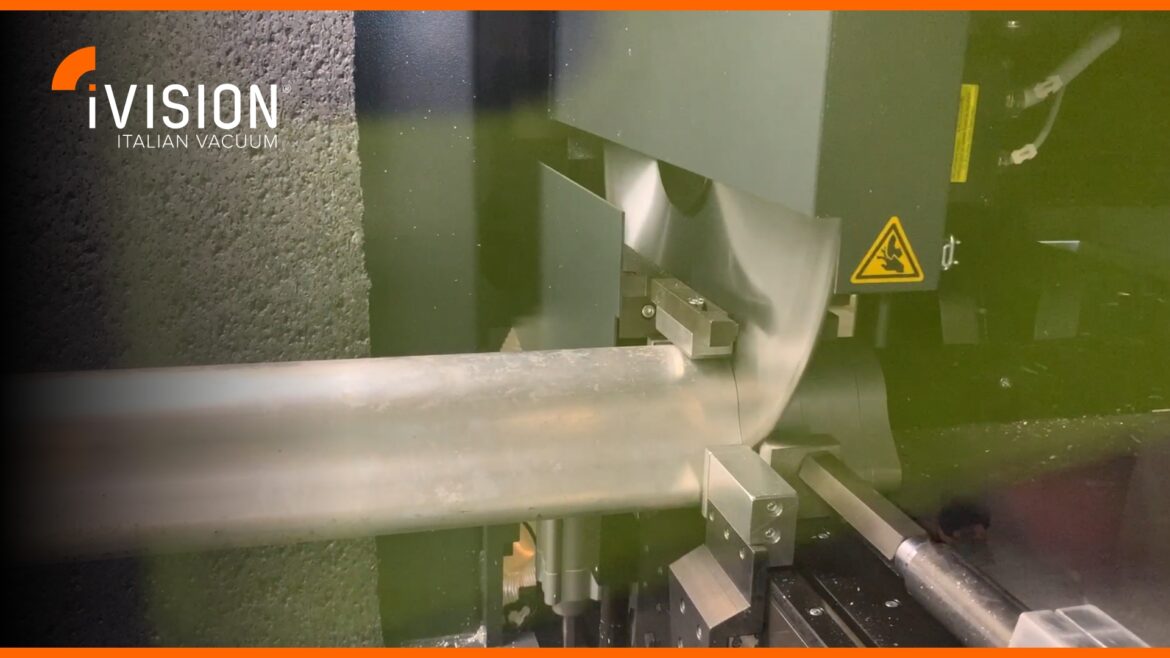
In the European heart of the automotive industry, in the German district of Stuttgart, there is a company that has been operating in the engineering sector for over 50 years. At the beginning of the 70’s, its founder started to explore the market of the machine tools: since then, the company has become an important reality for the production of machining centers for metalworking, including aluminum, dedicated to the automotive world. For this company, we designed industrial vacuum systems that could complete their machining centers, meeting the specific needs of their customers.
The needs of end customers
The companies that purchase machining centers from our customer have very high work rates. For this reason, they asked us for a solution able to suction up at least 1 m3 of aluminium chips per hour, without necessarily having to stop the entire production process to empty the collection container of the vacuum cleaner. In fact, their machines are subjected to three shifts, making it impossible to keep using standard industrial wheeled vacuum cleaners, which are insufficient to cover the amount of chips produced in such a short time. In fact, this system generates very long downtimes, with a consequent slowing down of the production rhythm.
Another need underlined by the end customers is the urgency to centralize the suction, so that the production waste can be recovered from many suctioning points. In this way, the production process is further speeded up, since it is not necessary to move the vacuum cleaner to the place where it is needed or to place one for each suctioning point.
The project
After carefully studying the needs listed above, the iVision Vacuum experts proposed a solution that perfectly matched the requirements of the companies in question. First, we designed a compact but powerful vacuum system that could suction the chips produced in continuous discharge from several points in the the customers’ machining centers. Once the main suction points had been identified, we carried out co-engineering activities to position the suction inlets in strategic positions with respect to blades, electrospindles or drills, in order to allow an optimal suction capacity.
The peculiarity of this system lies in a pressurized suction system that collects the chips and transports it to the collection point, conveying it through a rotary valve that releases the chips continuously. Under this rotary valve, the customer can place any container to deposit the production residues, thus choosing the capacity that best suits his production rhythms.
When the container is full, the operator is warned by an acoustic signal and the rotary valve stops momentarily: the operator can then remove the full container, replace it with the empty one and reactivate the discharge of chips through the rotary valve. During this process, however, the suction is not interrupted, but the material continues to accumulate. Once the suction is reactivated, the material suctioned in the meantime will be discharged into the collection container, restarting the normal work cycle.
The chip discharge point is also equipped with fill sensors, which activate as the material approaches the valve. These sensors alert the operator that the collection container will need to be replaced shortly through both a visual and audible alarm. To preserve the main vacuum filter there is a cyclonic pre-filter, able to separate the coarsest and heaviest chips.
“We are really satisfied with this new system, which has been specially designed to combine perfectly with our machining centers,” says the representative of our customer company. “Finally we can offer our customers a complete solution, saving them the trouble of emptying the vacuum containers every half hour, thus stopping the entire production cycle.”