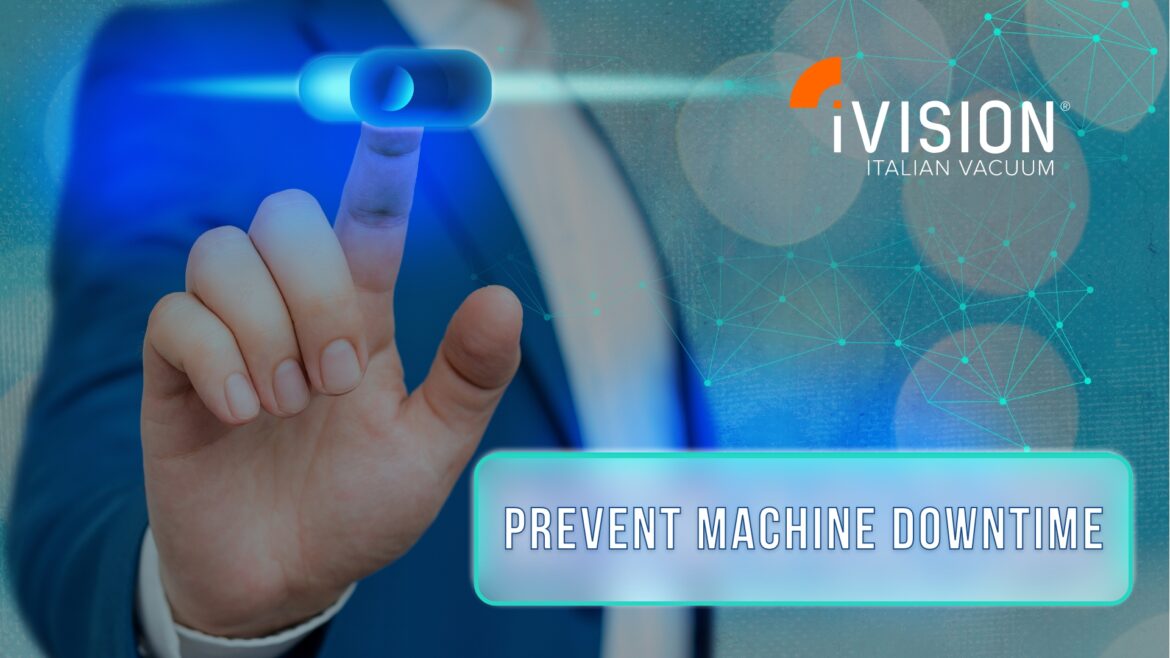
Machine downtime occurs when one or more machines become unproductive, causing significant damage to production and turnover targets. This situation happens for a variety of reasons, which are beyond the control of the worker or production line manager.
Although it is a very common problem, often underestimated, it can be prevented with Industry 4.0.
Downtime hidden costs
Before we discover all the benefits of Industry 4.0 and iVision Vacuum 4.0 connected related to machine downtime prevention, let’s delve into what are the hidden costs that the company incurs when production stops.
– The cost of lost production
If a company produces 600 items per hour, with a profit of 20 euros per item, one hour of downtime will cost it 12,000 euros.
– The cost of wages and utilities
When a piece of machinery suffers a breakdown, the employees on that specific production line are temporarily stopped or even obliged to work beyond normal working hours to restore the efficiency of the production cycle. This is the same for the costs of utilities; when a company is not producing, it still continues to pay business utility costs.
– Loss or damage of products
Especially when perishable goods are involved, downtime could cost the loss of raw material. Just think of the food industry, where the raw material have an expiration date, so they must be processed within a short period of time.
The above-mentioned costs are the same costs that a company has to bear when a piece of machinery that is as simple as indispensable fails: the industrial vacuum cleaner. When an industrial vacuum cleaner, connected to a production line, is damaged, a large amount of products may be lost.
For example in the PCB industry, if the aspirator stops working, it risks producing a damaged circuit due to residues of dust. The situation gets worse when no one has a chance to notice that the vacuum cleaner is not doing its job properly. In this case, you can risk to lose hundreds of electronic circuits, it means time and money. So, following the logic of “better to be safe than sorry,” we now delve into the features and benefits of 4.0 connected related to downtime prevention.
The features of 4.0 connected related to machine downtime prevention
4.0 connected is perfect for companies with multiple production units, organized with several interconnected machines located in multiple production areas.
The innovative vacuum cleaner from iVision Vacuum, becomes the ideal tool for optimizing processes and quality of work. Once connected to the company’s network, it “speaks” the same language as all other 4.0 machines and, like these, allows monitoring useful parameters to prevent its own downtime. This promotes better generalized control of the entire production cycle.
The warning notifications useful for preventing downtime of the 4.0 connected vacuum cleaner are:
– Performance status
– Filter wear and clogging status
– Inefficiency alerts
Benefits of 4.0 connected to machine downtime prevention
Thanks to its unique features, 4.0 connected makes it possible to reduce, to almost zero, its own downtime and the downtime of combined machines.
The benefits are:
– Ad hoc and preventive maintenance
With 4.0 connected, maintenance interventions can be largely anticipated and scheduled with the possibility of organizing production activity and avoiding any kind of interruption in the production cycle.
– Maintaining a stable production rhythm
When any machine inefficiencies are known ahead of time, timely intervention promotes the maintenance of a stable production rhythm.
– Less time to analyze performance and inefficiencies
The time taken by the operator, or the production line manager, to monitor the performance status of the vacuum cleaner is reduced to the visualization of the collected parameters. These, are visible thanks to the cloud signed iVision Vacuum, made available to the customer and usable from any type of device.
Notifications can be set up with reference to specific needs of the company, at the same time, iVision support is always careful to monitor any anomalies and notify the customer. This implies access to personalized support, even remotely.
– Safeguarding product integrity
Anticipating downtime also saves product integrity. In fact, as reported earlier, some products require consistently excellent operation of the vacuum machine. If this fails, the final result would be a damaged product.
Another feature of the 4.0 connected vacuum cleaner that, in a more general way, improves the quality of work is the HEPA filter. In this case, it is an improvement related primarily to the health of the people who work and the environment around them. The HEPA filter has a high filtering capacity and is certified to put highly filtered air back into the environment.